Have you ever wondered how silicone strips are made? The answer lies in a fascinating process called silicon extrusion. Let’s dive into what it is and why it matters.
Silicon extrusion is a manufacturing process where silicone material is forced through a die to create continuous strips or profiles. It’s widely used in industries like LED lighting, automotive, and medical devices. The process requires specialized machines and precise temperature control to achieve the desired product quality.
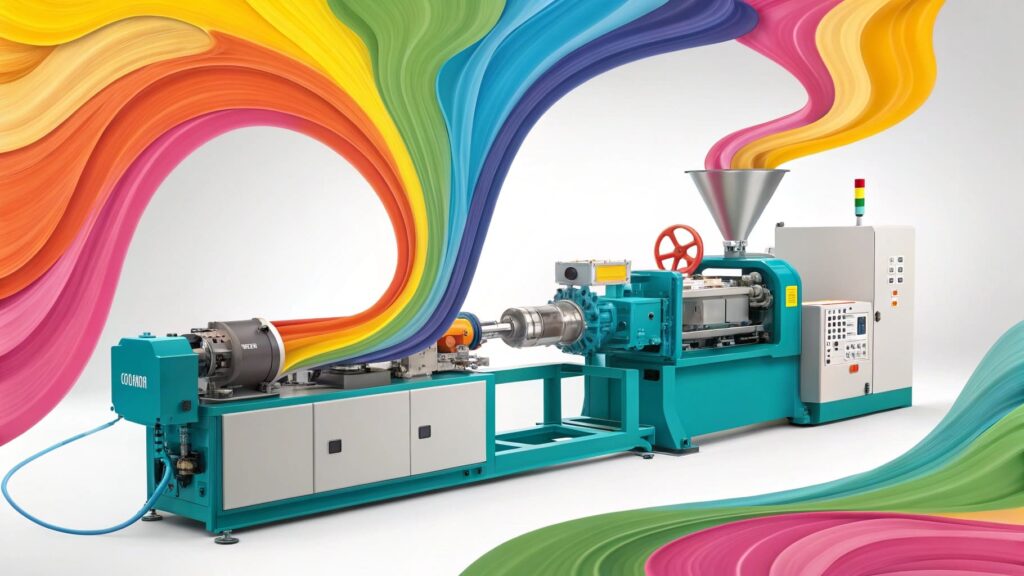
Now that you know the basics, let’s explore some common questions about silicon extrusion. Whether you’re a manufacturer or just curious, this guide will help you understand the process better.
Can silicone be extruded?
Yes, silicone can be extruded! But how does it work, and what makes it suitable for this process? Let’s break it down.
Silicone is highly suitable for extrusion due to its flexibility, heat resistance, and durability. The material is fed into an extruder, heated, and pushed through a die to form specific shapes like strips, tubes, or seals. This makes it ideal for applications requiring precision and consistency.
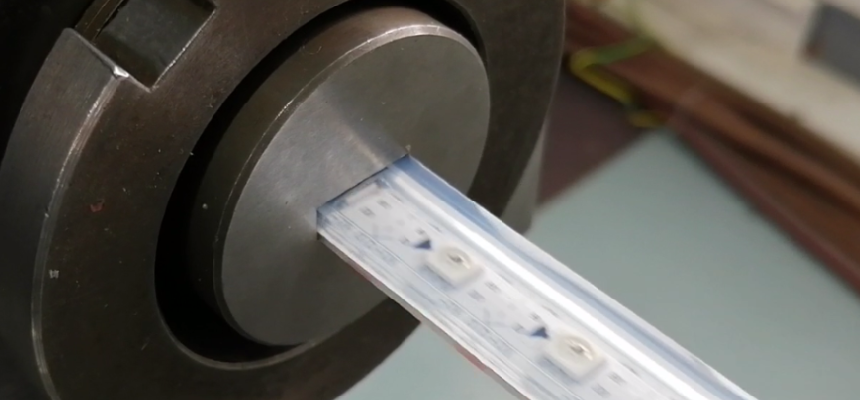
How Silicone Extrusion Works
Silicone extrusion involves several steps to transform raw silicone into finished products. Here’s a detailed look at the process:
- Material Preparation: Raw silicone is mixed with additives like color masterbatches and curing agents. This mixture ensures the final product has the desired properties, such as color, flexibility, and strength.
- Feeding the Extruder: The prepared silicone is fed into the extruder machine. The machine consists of a barrel, screw, and die. The screw rotates to push the material forward while heating it to a specific temperature.
- Heating and Shaping: As the silicone moves through the barrel, it is heated to a precise temperature. This makes the material soft and pliable, allowing it to be shaped as it passes through the die.
- Cooling and Curing: After exiting the die, the extruded silicone is cooled and cured. This step ensures the material retains its shape and achieves the desired hardness.
Applications of Silicone Extrusion
Silicone extrusion is used in various industries due to its versatility. Here are some common applications:
Industry | Application | Benefits of Silicone Extrusion |
---|---|---|
LED Lighting | LED strip covers | Heat resistance, flexibility |
Automotive | Seals and gaskets | Durability, weather resistance |
Medical Devices | Tubing and seals | Biocompatibility, precision |
Construction | Weatherproofing strips | Longevity, UV resistance |
Silicone extrusion is a reliable method for producing high-quality products. Whether you need simple strips or complex profiles, this process can meet your needs.
What temperature is silicone extrusion?
Temperature plays a crucial role in silicone extrusion. But what’s the ideal range, and why does it matter? Let’s find out.
The temperature for silicone extrusion typically ranges between 120°C and 180°C. This range ensures the silicone is soft enough to extrude but not so hot that it degrades. Precise temperature control is essential for achieving consistent product quality.
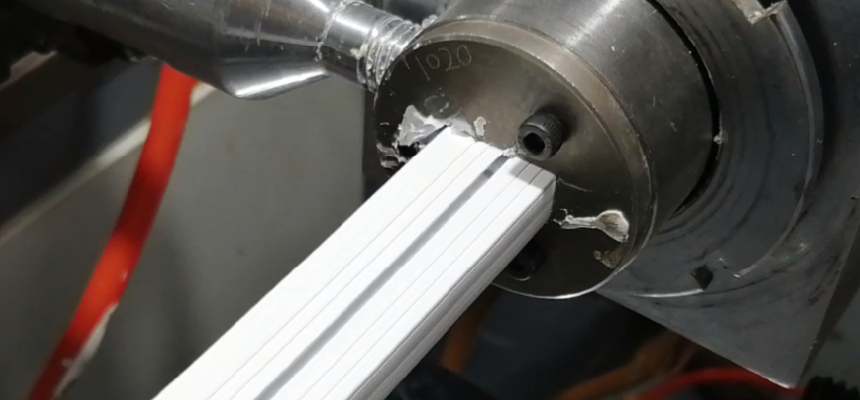
Why Temperature Matters in Silicone Extrusion
Temperature control is critical in silicone extrusion[^1] for several reasons:
Material Consistency: Silicone must be heated to the right temperature to achieve the right viscosity. If it’s too cold, the material won’t flow smoothly. If it’s too hot, it can degrade and lose its properties.
Product Quality: Consistent temperature ensures the extruded silicone has uniform thickness, shape, and texture. This is especially important for applications like LED strips, where precision is key.
Machine Efficiency: Proper temperature settings reduce wear and tear on the extruder machine. It also minimizes the risk of defects, saving time and materials.
[^1]: Understanding the role of temperature in silicone extrusion can significantly improve product quality and machine efficiency.
Temperature Settings for Different Applications
The ideal temperature can vary depending on the type of silicone and the desired product. Here’s a breakdown:
Silicone Type | Temperature Range (°C) | Application Example |
---|---|---|
Standard Silicone | 120-150 | Seals, gaskets |
High-Temperature | 150-180 | LED strip covers, automotive parts |
Medical-Grade | 130-160 | Tubing, seals for medical devices |
Tips for Temperature Control
- Use a high-quality extruder machine with precise temperature controls.
- Monitor the temperature throughout the process to avoid fluctuations.
- Adjust the settings based on the silicone material and product requirements.
By understanding the importance of temperature, you can optimize your silicone extrusion process for better results.
How is silicon turned into rubber?
Silicone rubber is a versatile material used in countless products. But how is it made? Let’s explore the transformation process.
Silicone rubber is created by mixing raw silicone with curing agents and additives. The mixture is then heated and shaped through processes like extrusion or molding. This transforms it into a durable, flexible material suitable for various applications.
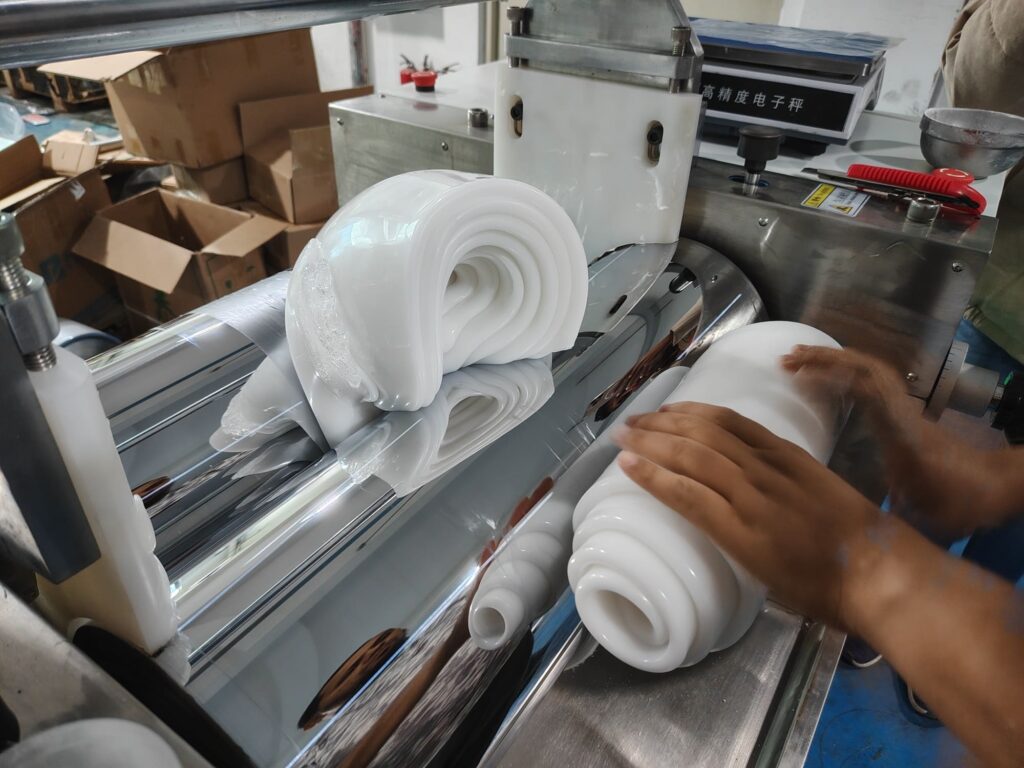
The Process of Making Silicone Rubber
Turning silicone into rubber involves several steps:
Raw Material Preparation: Raw silicone is combined with curing agents[^1], colorants, and other additives. These ingredients determine the final properties of the rubber, such as hardness, color, and flexibility.
Mixing and Compounding: The mixture is thoroughly blended to ensure uniformity. This step is crucial for achieving consistent quality in the final product.
Heating and Curing: The mixed silicone is heated to activate the curing agents. This causes the material to harden and take on its rubber-like properties. The curing process can be done through extrusion, molding, or other methods[^2].
Shaping and Finishing: Once cured, the silicone rubber is shaped into the desired form. This could be strips, tubes, seals, or other profiles. The final product is then cooled and inspected for quality.
[^1]: Understanding curing agents is crucial for controlling the hardness and flexibility of silicone rubber, essential for product quality.
[^2]: Exploring these methods helps in selecting the right curing process for specific silicone rubber applications, optimizing production efficiency.
Applications of Silicone Rubber
Silicone rubber is used in a wide range of industries due to its unique properties. Here are some examples:
Industry | Application | Benefits of Silicone Rubber |
---|---|---|
Electronics | Keypads, seals | Heat resistance, electrical insulation |
Healthcare | Medical tubing, implants | Biocompatibility, flexibility |
Automotive | Gaskets, hoses | Durability, weather resistance |
Consumer Goods | Kitchenware, phone cases | Non-toxic, easy to clean |
Why Choose Silicone Rubber?
Silicone rubber offers several advantages over other materials:
- It can withstand extreme temperatures, from -60°C to 230°C.
- It’s highly flexible and resistant to tearing.
- It’s non-toxic and safe for use in medical and food-related applications.
By understanding how silicone is turned into rubber, you can appreciate its versatility and value in manufacturing.
What is the difference between extruded and molded rubber?
Extruded and molded rubber are both popular manufacturing methods. But what sets them apart, and which one is right for your needs? Let’s compare.
Extruded rubber is created by forcing material through a die to form continuous shapes, while molded rubber is shaped using a mold cavity. Extrusion is ideal for long, uniform products, while molding is better for complex, detailed designs.

Extruded Rubber: Pros and Cons
Extruded rubber[^1] is made by pushing silicone or other rubber materials through a die. Here’s what you need to know:
Advantages:
Cost-Effective: Extrusion is generally cheaper for producing long, continuous shapes.
Consistency: The process ensures uniform thickness and shape[^2] throughout the product.
Versatility: Extruded rubber[^1] can be cut to any length, making it suitable for various applications.
[^1]: Discover the cost-effectiveness, consistency, and versatility of extruded rubber, making it ideal for various applications.
[^2]: Understand the significance of uniform thickness and shape in ensuring product consistency and performance in extruded rubber applications.
Disadvantages:
- Limited Complexity: Extrusion is less suitable for intricate designs or detailed patterns.
- Post-Processing: Extruded products may require additional cutting or finishing.
Molded Rubber: Pros and Cons
Molded rubber is created by placing material into a mold cavity and applying heat and pressure. Here’s how it compares:
Advantages:
- Complex Shapes: Molding allows for intricate designs and detailed features.
- High Precision: The process ensures accurate dimensions and tight tolerances.
- No Post-Processing: Molded products are usually ready to use after curing.
Disadvantages:
- Higher Cost: Molding is more expensive due to the need for custom molds.
- Limited Length: Molded products are typically shorter and more compact.
Choosing the Right Method
The choice between extrusion and molding depends on your product requirements. Here’s a quick guide:
Feature | Extruded Rubber | Molded Rubber |
---|---|---|
Shape Complexity | Simple, uniform shapes | Complex, detailed designs |
Production Volume | High volume, continuous production | Lower volume, batch production |
Cost | Lower cost | Higher cost |
Applications | Seals, gaskets, tubing | Keypads, custom parts, intricate seals |
By understanding the differences, you can choose the best method for your manufacturing needs.
Conclusion
Silicon extrusion is a versatile and efficient process for creating high-quality silicone products. Whether you’re producing LED strips, seals, or medical tubing, understanding the process can help you achieve better results.