LED extrusions are essential in modern lighting. They shape and protect LED strips, ensuring durability and performance. Let’s dive into what makes them unique.
An LED extrusion is a profile made from materials of silicone, designed to house and protect LED strips. It enhances heat dissipation, improves light diffusion, and ensures the longevity of LED lighting systems.
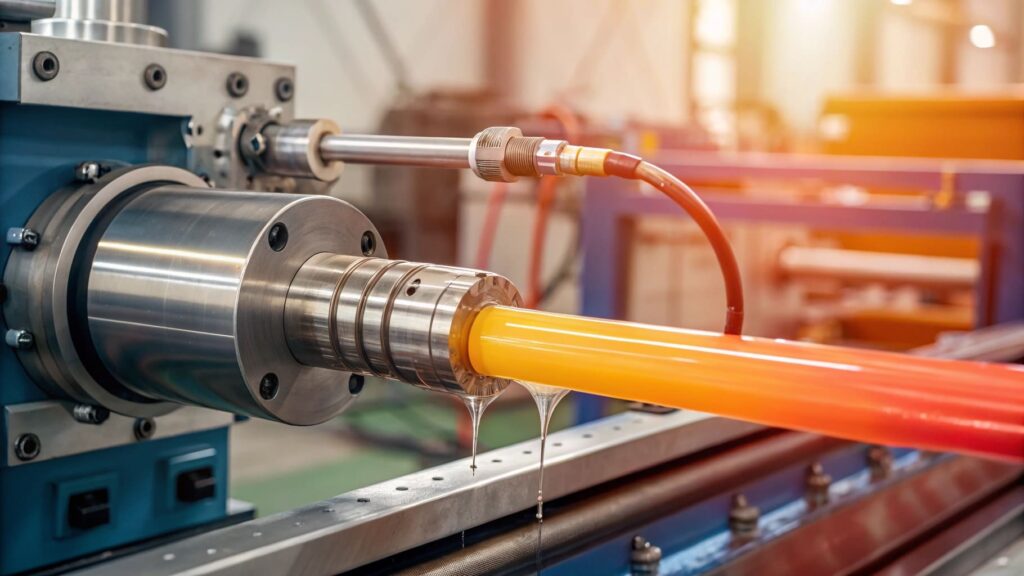
Now that we understand what LED extrusions are, let’s explore how to choose the right silicone extrusion production line, solder LED strips, and more.
How to choose a silicon extrusion production line?
Choosing the right silicone extrusion production line can be challenging. The key is to match your needs with the right equipment.
To choose a silicone extrusion production line, first determine the type of LED strip you want to produce. Single-color strips require one extruder, while multi-color strips need multiple extruders. The cost and setup vary based on your production goals.
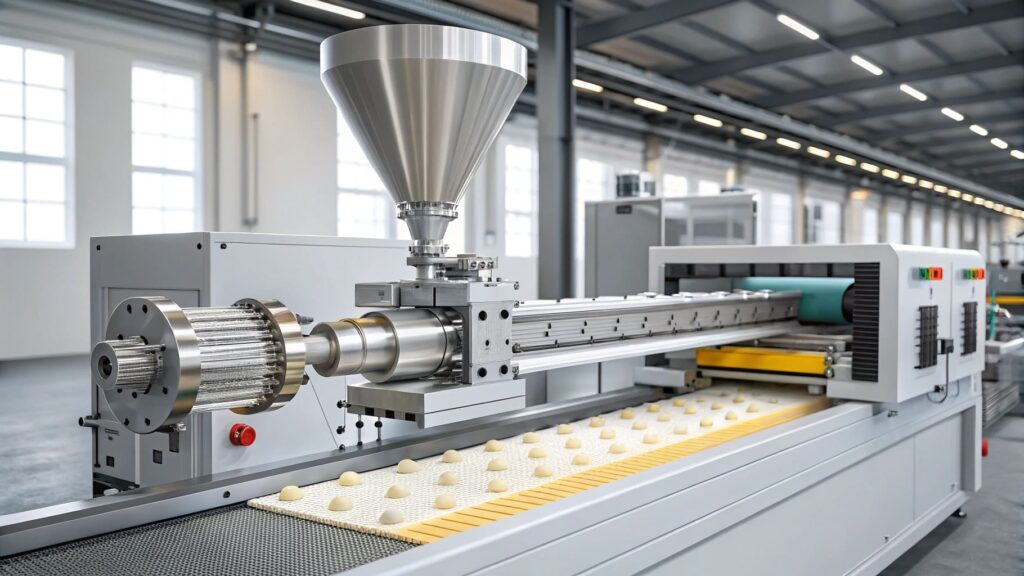
Understanding Your Production Needs
Before investing in a silicone extrusion production line, it’s crucial to understand your production requirements. Here’s a breakdown:
Strip Type | Extruders Needed | Cost | Setup Complexity |
---|---|---|---|
Single-color | 1 | Low | Simple |
Two-color | 2 | Medium | Moderate |
Three-color | 3 | High | Complex |
Key Considerations
- Production Volume: Higher volumes may require more advanced machinery and engineered workers.
- Material supply continuity: Ensure the silicone and additives supply chain is strongly supported.
- Space Requirements: A typical setup needs a factory space of at least 35×5 meters.
- Labor: You’ll need around five workers to operate the production line efficiently.
Support and Training
When you purchase a machine from us, we offer comprehensive support. You can send your engineers to our factory for training, or we can send our engineers to your facility for installation and trial production. Our goal is to ensure you can handle full production confidently.
Lead Time and Shipping
The manufacturing lead time is approximately 35 working days. Shipping typically takes 10-35 days, depending on your location. We ensure the entire process is smooth, from production to delivery.
How do you solder LED strips?
Soldering LED strips might seem tricky, but with the right tools and techniques, it’s straightforward.
Soldering LED strips involves connecting wires to the strip’s copper pads using a soldering iron and solder. Proper insulation and heat management are crucial to avoid damage.
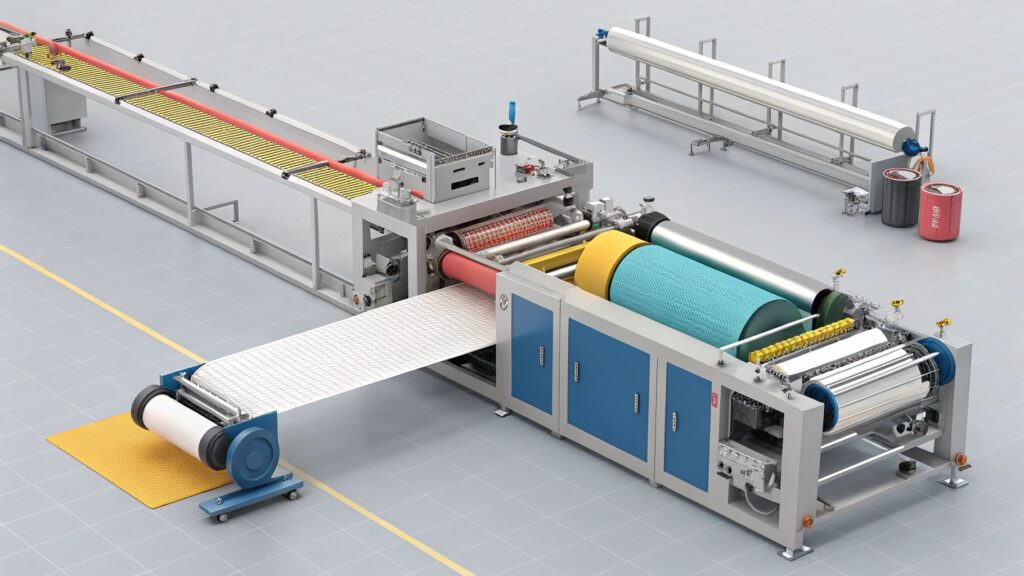
Tools and Materials Needed
To solder LED strips, you’ll need:
- A soldering iron (30-60 watts) or advanced soldering machine
- Solder wire (lead-free is recommended)
- Flux (to improve solder flow)
- Heat shrink tubing (for insulation)
- Wire cutters and strippers
Step-by-Step Guide
- Prepare the LED Strip: Cut the strip to the desired length at the marked cutting points.
- Strip the Wires: Strip about 5mm of insulation from the wires you’ll connect.
- Apply Flux: Apply a small amount of flux to the copper pads on the LED strip.
- Tin the Pads: Heat the copper pads with the soldering iron and apply a small amount of solder to each pad.
- Connect the Wires: Place the stripped wires onto the tinned pads and heat them with the soldering iron until the solder melts and bonds the wire to the pad.
- Insulate the Connections: Slide heat shrink tubing over the soldered connections and use a heat gun to shrink the tubing, ensuring the connections are insulated.
Tips for Success
- Avoid Overheating: Excessive heat can damage the LED strip. Work quickly and efficiently.
- Check Polarity: Ensure the positive and negative wires are correctly connected to avoid short circuits.
- Test the Connection: After soldering, test the LED strip to ensure it works correctly before final installation.
Do LED strips use a lot of electricity?
Many people worry about the energy consumption of LED strips. The good news is, they are highly efficient.
LED strips are energy-efficient, consuming significantly less electricity than traditional lighting. On average, an LED strip uses about 4-14 watts per meter, making it a cost-effective lighting solution.
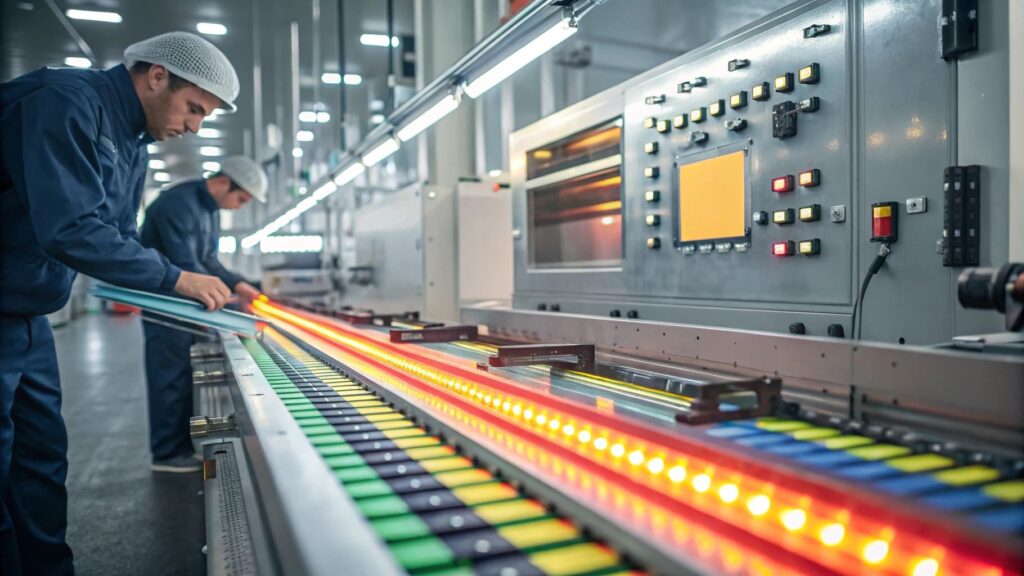
Understanding Energy Consumption
LED strips are designed to be energy-efficient. Here’s a comparison of energy consumption:
Lighting Type | Power Consumption (Watts per Meter) |
---|---|
LED Strip | 4-14 |
Incandescent Bulb | 40-100 |
Fluorescent Tube | 18-40 |
Factors Affecting Energy Use
- LED Density: Higher-density strips (more LEDs per meter) consume more power.
- Brightness: Brighter strips require more energy.
- Color: RGB strips may use slightly more power due to the additional LEDs for color mixing.
Cost Savings
LED strips can save you money on electricity bills. For example, a 5-meter LED strip running for 8 hours a day consumes about 0.04-0.14 kWh per day, costing just a few cents.
Environmental Impact
LED strips are not only cost-effective but also environmentally friendly. They produce less heat and have a longer lifespan, reducing waste and energy consumption.
What material is a LED strip made of?
The materials used in LED strips play a crucial role in their performance and durability.
LED strips are typically made of a flexible PCB (printed circuit board), copper conductive traces, LED chips, and a silicone coating for protection. These materials ensure flexibility, conductivity, and durability.
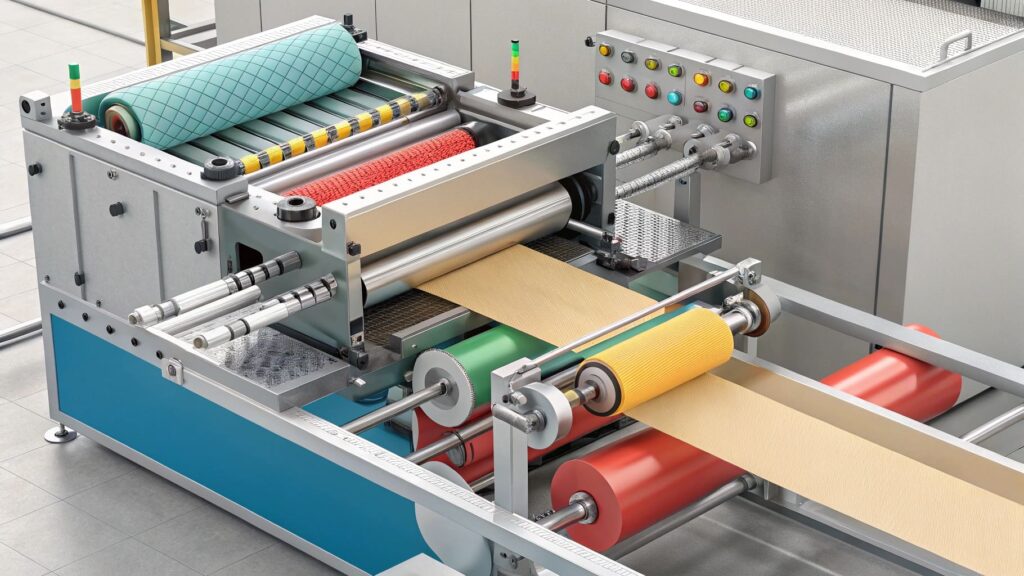
Components of an LED Strip
- Flexible PCB: The base of the LED strip, usually made of polyimide, provides flexibility and durability.
- Copper Traces: These conductive paths connect the LED chips and other components, ensuring electrical conductivity.
- LED Chips: The light-emitting diodes (LEDs) are mounted on the PCB. They come in various sizes and colors.
- Silicone Coating: A protective layer that shields the components from moisture, dust, and physical damage.
Material Properties
Material | Function | Properties |
---|---|---|
Flexible PCB | Base material | Flexible, durable, heat-resistant |
Copper Traces | Electrical conductivity | High conductivity, corrosion-resistant |
LED Chips | Light emission | Energy-efficient, long lifespan |
Silicone Coating | Protection | Waterproof, dustproof, UV-resistant |
Customization Options
We offer a variety of materials to meet your specific needs. Whether you need standard silicone or specialized additives, we can provide the right materials at competitive prices.
Conclusion
LED extrusions and strips are versatile, energy-efficient, and easy to customize. With the right knowledge and equipment, you can create high-quality lighting solutions tailored to your needs.