Have you ever wondered if silicone can be melted and reshaped? This question is crucial for industries relying on silicone products. Let’s dive into the science and practicality behind it.
Yes, silicone can be reshaped. Silicone is a versatile material that can be heated to a high temperature, allowing it to be molded into new forms. This process is essential in industries like manufacturing and electronics, where custom shapes are often needed.
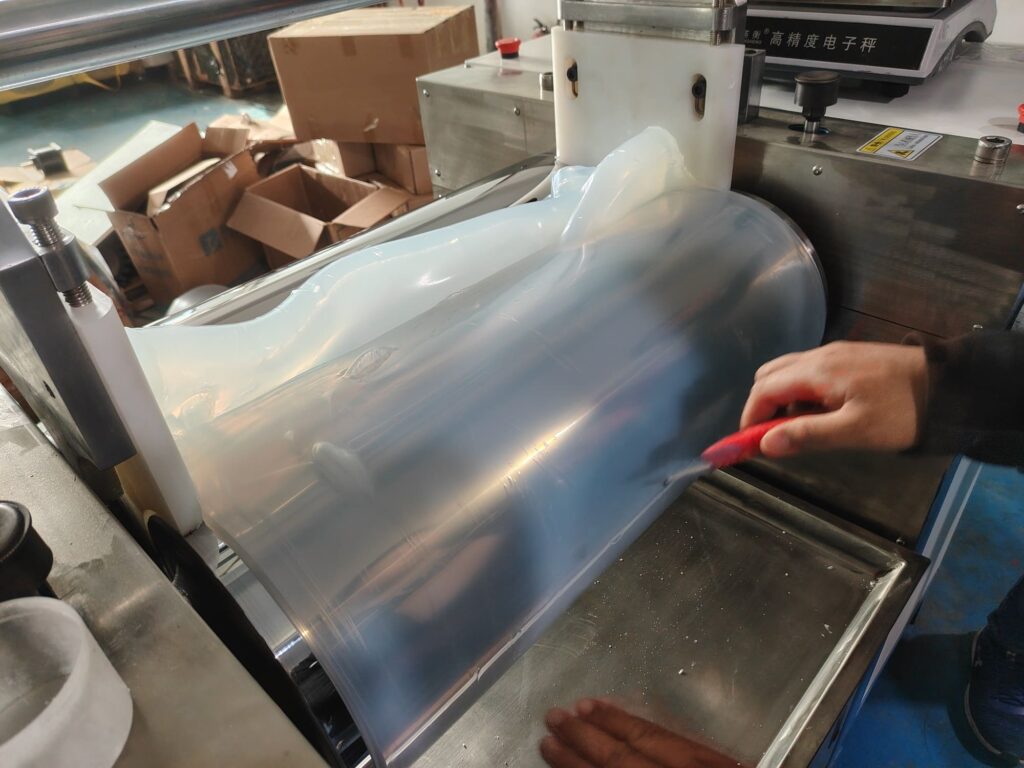
Understanding how silicone behaves under heat is just the beginning. Let’s explore more about its properties and applications in different manufacturing processes.
Can silicone be compressed?
Compression is another method used in silicone processing. But can silicone really be compressed effectively?
Silicone can be compressed, but it requires specific conditions. Compression molding is a common technique where silicone is placed in a mold and subjected to high pressure and heat to form the desired shape.
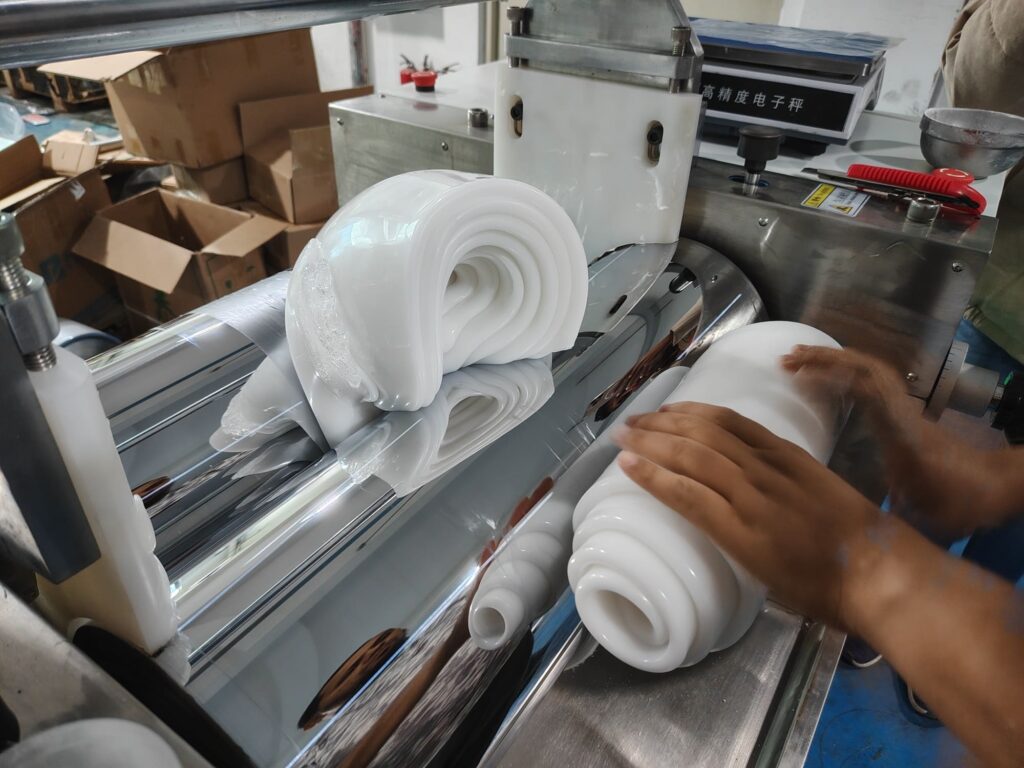
Dive deeper Paragraph:
Understanding Compression Molding
Compression molding is a widely used method for shaping silicone. Here’s a breakdown of how it works:
- Material Preparation: Silicone is prepared in a raw form, often as a sheet or preform.
- Mold Setup: The silicone is placed into a mold cavity.
- Application of Heat and Pressure: The mold is closed, and both heat and pressure are applied. This causes the silicone to flow and fill the mold.
- Cooling and Ejection: After the silicone has taken the shape of the mold, it is cooled and then ejected.
Advantages of Compression Molding
- Cost-Effective: It is generally cheaper than other molding techniques.
- Suitable for Large Parts: Ideal for producing large, relatively simple shapes.
- Material Efficiency: Minimizes waste as excess material can often be reused.
Disadvantages of Compression Molding
- Limited Complexity: Not suitable for highly detailed or complex parts.
- Longer Cycle Times: The process can be slower compared to other methods like injection molding.
Comparing Compression Molding with Other Techniques
Feature | Compression Molding | Injection Molding |
---|---|---|
Cost | Lower | Higher |
Cycle Time | Longer | Shorter |
Part Complexity | Low to Medium | High |
Material Waste | Minimal | Moderate |
Understanding these differences helps in choosing the right method for your specific needs.
Is extrusion better than injection molding?
leading paragraph:
When it comes to shaping silicone, extrusion and injection molding are two popular methods. But which one is better?
snippet paragraph:
Extrusion and injection molding each have their own advantages. Extrusion is ideal for creating continuous shapes like tubes and strips, while injection molding is better for complex, detailed parts.
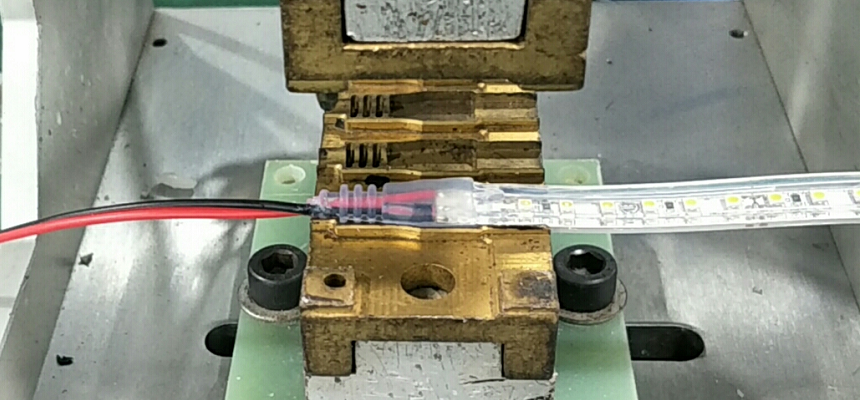
Dive deeper Paragraph:
Extrusion vs. Injection Molding
Extrusion
Extrusion is a process where silicone is forced through a die to create a continuous shape. This method is commonly used for producing items like tubing, seals, and strips.
Advantages of Extrusion:
- Continuous Production: Ideal for long, uniform products.
- Cost-Effective for High Volumes: Lower cost per unit for large quantities.
- Flexibility: Can produce a wide range of shapes and sizes.
Disadvantages of Extrusion:
- Limited Complexity: Not suitable for intricate designs.
- Material Limitations: Some materials may not extrude well.
Injection Molding
Injection molding involves injecting molten silicone into a mold cavity. This method is used for creating complex, detailed parts.
Advantages of Injection Molding:
- High Precision: Capable of producing intricate designs.
- Fast Cycle Times: Efficient for high-volume production.
- Material Versatility: Works well with a variety of materials.
Disadvantages of Injection Molding:
- Higher Initial Cost: Expensive molds and machinery.
- Material Waste: More waste compared to extrusion.
Choosing the Right Method
Feature | Extrusion | Injection Molding |
---|---|---|
Best For | Continuous Shapes | Complex Parts |
Cost | Lower | Higher |
Cycle Time | Longer | Shorter |
Part Complexity | Low to Medium | High |
Understanding these differences helps in selecting the right method for your specific needs.
Can natural rubber be extruded?
leading paragraph:
Natural rubber is another material widely used in manufacturing. But can it be extruded like silicone?
snippet paragraph:
Yes, natural rubber can be extruded. The process involves heating the rubber and forcing it through a die to create the desired shape, similar to silicone extrusion.
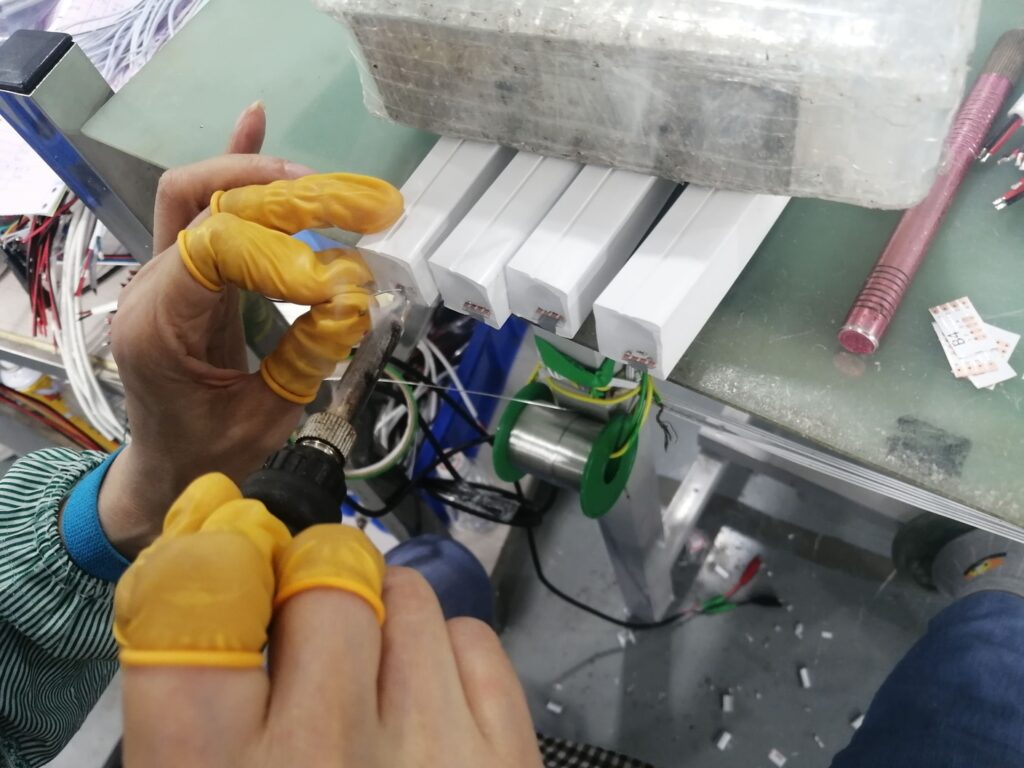
Dive deeper Paragraph:
Extrusion of Natural Rubber
Extruding natural rubber involves several steps:
- Material Preparation: Natural rubber is mixed with additives to improve its properties.
- Heating: The rubber is heated to make it pliable.
- Extrusion: The heated rubber is forced through a die to create the desired shape.
- Cooling and Curing: The extruded rubber is cooled and then cured to set its final form.
Advantages of Extruding Natural Rubber
- Versatility: Can produce a wide range of shapes and sizes.
- Cost-Effective: Lower cost per unit for large quantities.
- Material Efficiency: Minimizes waste as excess material can often be reused.
Disadvantages of Extruding Natural Rubber
- Limited Complexity: Not suitable for intricate designs.
- Material Limitations: Some additives may not extrude well.
Comparing Natural Rubber and Silicone Extrusion
Feature | Natural Rubber | Silicone |
---|---|---|
Material Properties | Elastic, Durable | Flexible, Heat Resistant |
Extrusion Process | Similar | Similar |
Applications | Tires, Seals | Medical Devices, Electronics |
Understanding these differences helps in choosing the right material for your specific needs.
What is the difference between vulcanized and molded rubber?
leading paragraph:
Vulcanized and molded rubber are terms often used interchangeably, but they refer to different processes. What sets them apart?
snippet paragraph:
Vulcanized rubber undergoes a chemical process to improve its strength and elasticity, while molded rubber is shaped using heat and pressure. Both methods have unique applications and benefits.
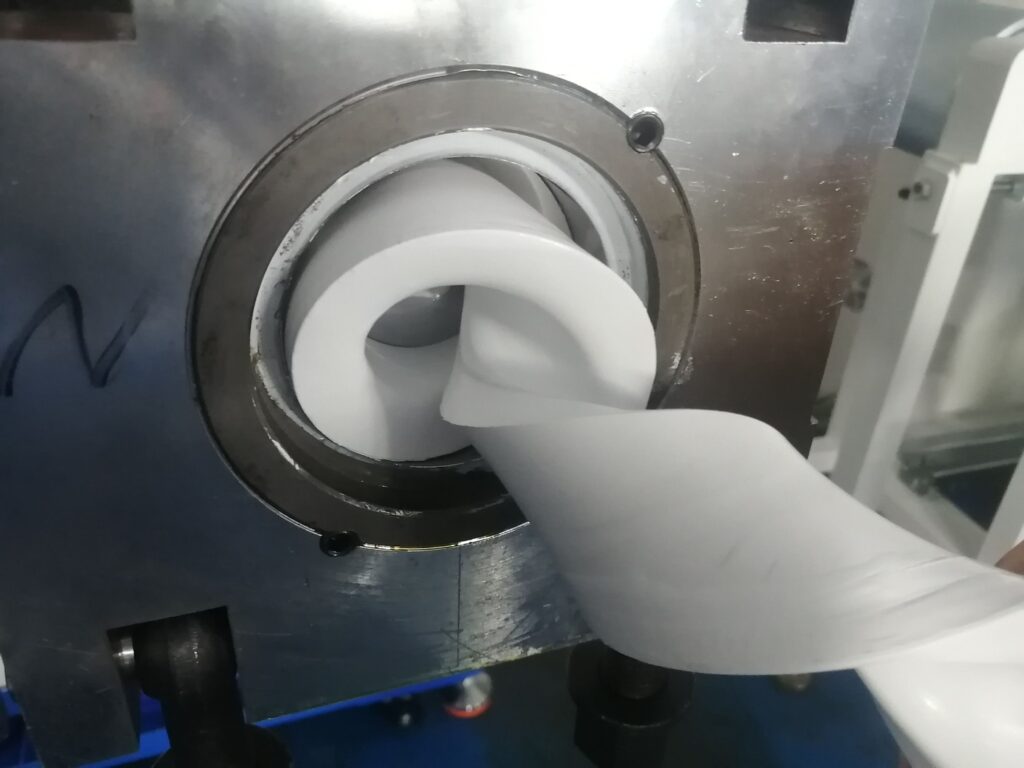
Dive deeper Paragraph:
Understanding Vulcanized Rubber
Vulcanization is a chemical process that involves adding sulfur or other curatives to rubber. This process enhances the rubber’s properties, making it more durable and elastic.
Advantages of Vulcanized Rubber:
- Improved Strength: More resistant to wear and tear.
- Enhanced Elasticity: Better flexibility and resilience.
- Heat Resistance: Can withstand higher temperatures.
Disadvantages of Vulcanized Rubber:
- Complex Process: Requires precise control of temperature and time.
- Cost: More expensive due to the additional chemicals and process.
Understanding Molded Rubber
Molded rubber is shaped using heat and pressure. This method is used to create a wide range of products, from simple gaskets to complex automotive parts.
Advantages of Molded Rubber:
- Versatility: Can produce a wide range of shapes and sizes.
- Cost-Effective: Lower cost per unit for large quantities.
- Material Efficiency: Minimizes waste as excess material can often be reused.
Disadvantages of Molded Rubber:
- Limited Complexity: Not suitable for intricate designs.
- Material Limitations: Some materials may not mold well.
Comparing Vulcanized and Molded Rubber
Feature | Vulcanized Rubber | Molded Rubber |
---|---|---|
Process | Chemical | Heat and Pressure |
Strength | High | Medium |
Elasticity | High | Medium |
Applications | Tires, Industrial | Gaskets, Automotive |
Understanding these differences helps in selecting the right method for your specific needs.
Conclusion
Choosing the right method and material for your silicone or rubber products is crucial. Whether it’s extrusion, injection molding, or vulcanization, each has its own benefits and applications.